What are Conformal Coatings?
UV and conformal coatings are polymer based films that are applied to most types of electronic devices such as printed circuit boards. Conformal coatings can be used to create a seal tight, hydrophobic layer of protection that would otherwise harm the sensitive components. All electronic hardware is susceptible to damage from harsh elements such as moisture, salt, drastic temperature, ultra-violet light, and many other harsh environments. AIT’s conformal coating solutions can be specifically tailored for your products based on your needs making us of the top suppliers in the industry.
Difference between Standard and UV coatings
Similar to standard conformal coatings, UV specific coatings have various additive properties. AIT’s UV coatings have an impressive curing time of only a few seconds when exposed to certain intensities of UV light making it very suitable for coating electronics. In addition, UV Resistant coatings block harmful UV rays which can add a extra layer of protection. Finally, UV Florescence can be added to the coating. UV Florescence glows under UV light allowing for an easy verification and inspection of the material and where it was applied.
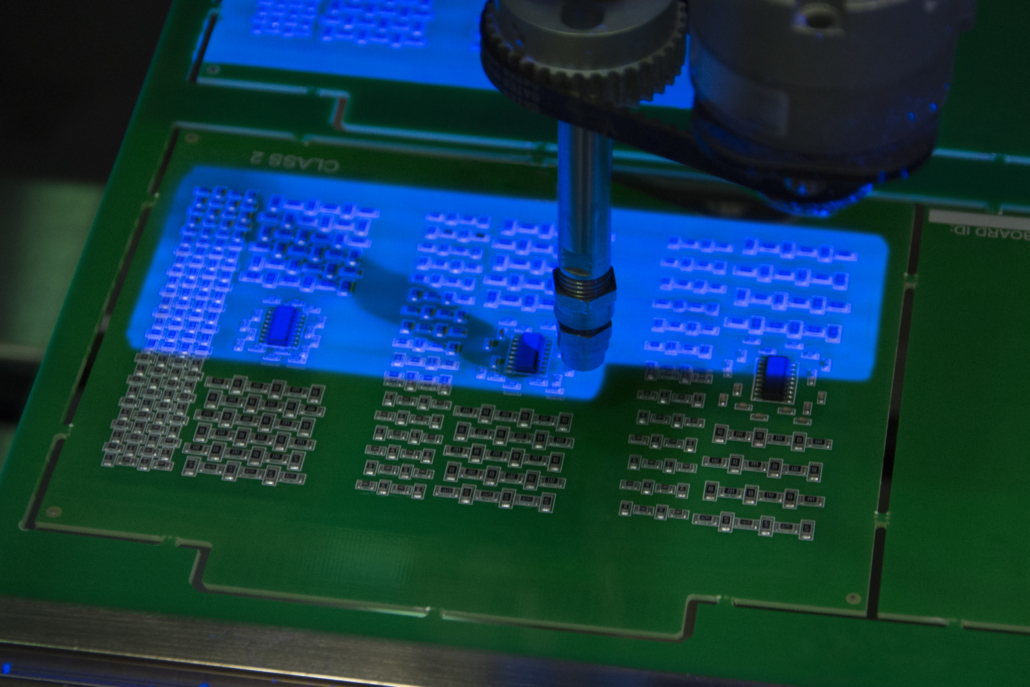
How are they important?
How important are conformal coatings to the modern era? Conformal coatings are very important for the industry due to it its versatile nature. Special materials are used to coat various products which provide protection against water, moisture, salt, chemicals, temperature, UV light and many other specific variables based on the material properties.
Conformal coatings are used in…
- Aeronautics/ Aerospace Industry
- Automobile Industry
- Consumer Products
- LED Industry
- Marine Industry
- Military Industry
- Power/ Energy Industry
Electronics can be found in almost every industry. Depending on the industry involved, the applied materials can vary on task or protection required. Conformal coatings stand as one of the most effective yet versatile solutions to protecting electronics. From consumer products such as smart phone and LED’s, to marine and military applications, and even within the aerospace industry, conformal coatings have proven to be the best solution.
Methods of application
They can be applied using various different techniques which are determined by a wide range of factors. AIT helps its clients determine the correct product for their needs while simultaneously determining the best method of application. Applying certain types of UV and conformal coatings incorrectly, especially a custom solution, can drastically change the effectiveness of the coating.
Application techniques:
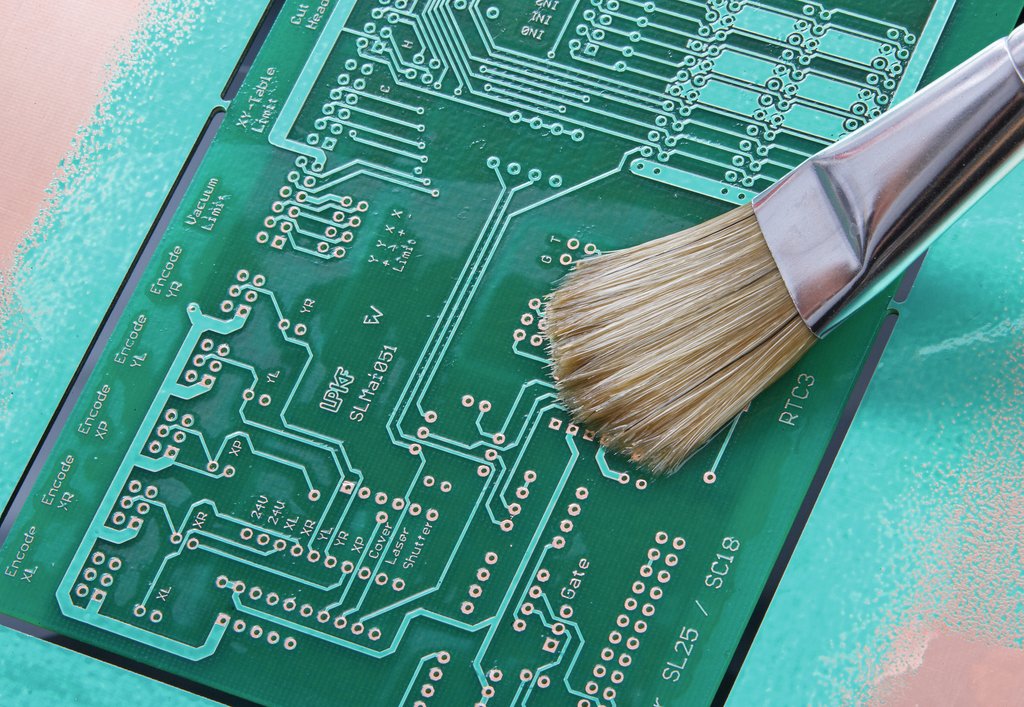
Brush Coating
Brush coating is a manual process of applying material to the electronics using a brush. It is an extremely cost efficient way of applying coatings to small scale products. Accuracy and consistency of the coating will depend on the skill and technique of the person applying it.
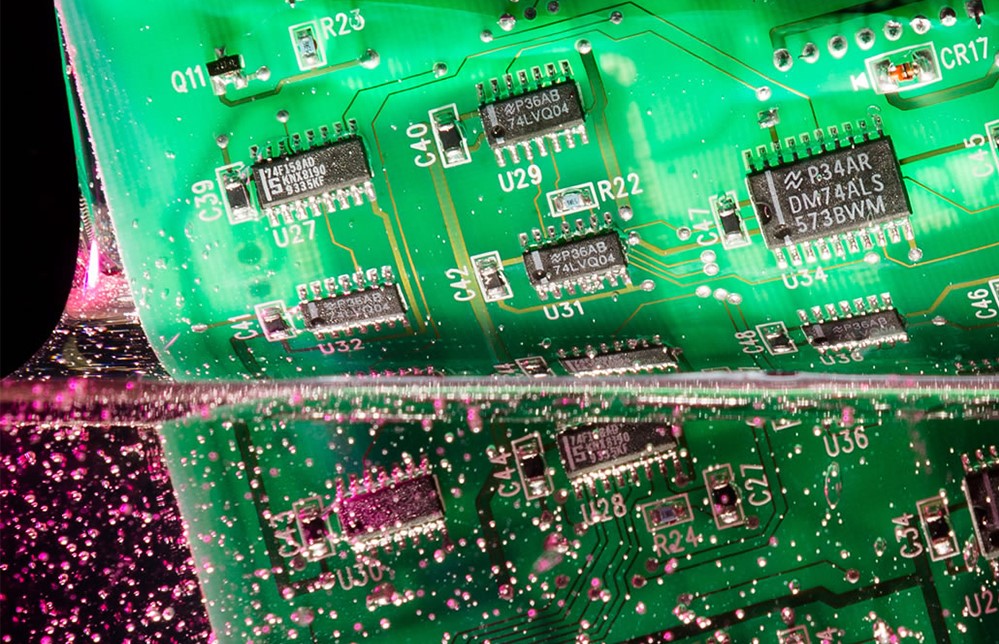
Dip Coating
Dip coating uses a mechanical device to physically dip the entire electronic or printed circuit board (PCB). Dipping is very effective if the entirety of the board needs to be covered. Some drawbacks include using a lower viscosity material that will not be suitable for PCB’s with components that are very close to each other. Very accurate masking may also be needed if full a full coverage is not necessary.
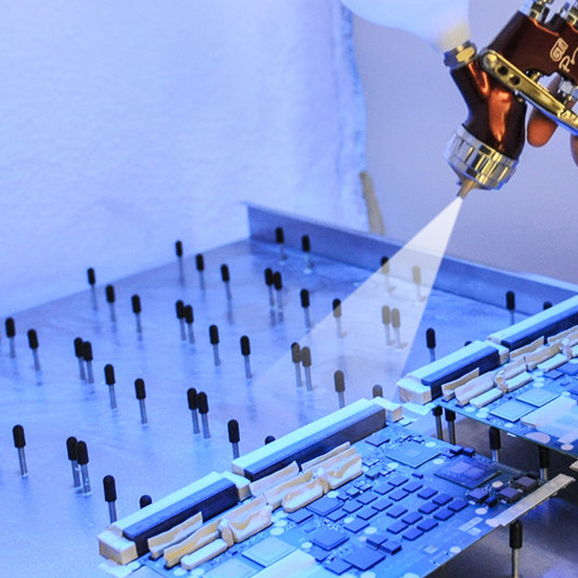
Spray Coating
Spray coating can be applied by hand or by machine depending on the size and cost of the project. By hand, it is typically applied via aerosol however a coating can also be applied with a professional spray gun in a spray room. Using a spray gun requires special skill and technique but quality is dramatically improved from standard aerosol applications.
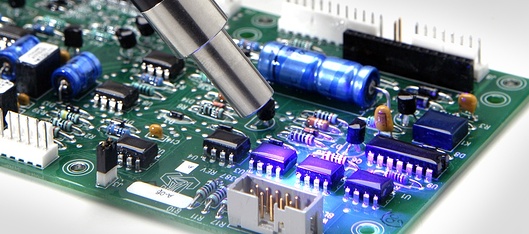
Selective Coating
Selective coating uses a machine that is specifically programmed to “selectively” coat only certain parts of the electronic device or PCB. Selective coating tends to be the most expensive however using this method also requires less masking and the coatings are more consistent than when applied by hand. The machine can also precisely coat certain areas and can be replicated with ease on similar electronic devices if needed.